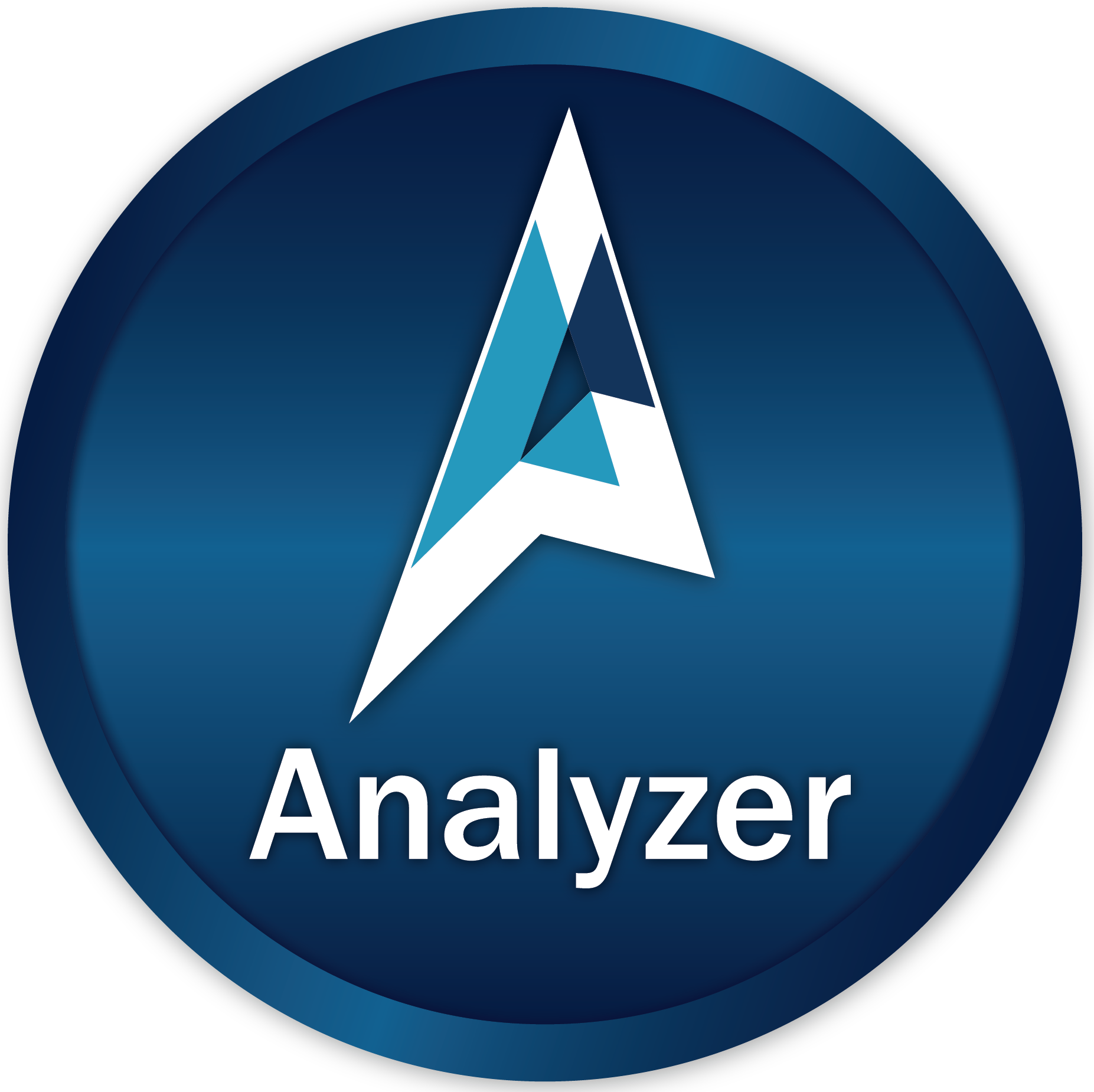
Analyzer, part of the Auxilium Suite is a modelling and analysis decision support tool.
When designing and managing a system or asset, the primary business driver is to reduce the cost of ownership while maximizing operational readiness. The challenge of cost-effective equipment support is pushed to the limits. Two of the most desired objectives of equipment ownership are: reduce operating costs and increase equipment availability.
Analyzer uses recognised processes and analytical methods to develop, store and evaluate information about operational equipment and the support environment, to maximize operational efficiency.
Analyzer has been a tool of choice for many customers and various applications for over 30 years. Over this time users have recognized the many benefits from using this flexible and intuitive modelling environment.
-
a supportability engineering modelling and simulation tool that analyses support solutions for complex products, including multi-indenture logistics structures
-
a modern technology product that simplifies the analysis process and supports many current data transfer standards
-
an extensive and user definable dashboard for data-driven decision making
-
identifies preferred product sustainment strategies through options analysis
-
applies sensitivity and risk analyses to improve awareness of variance and data quality impacts and of major cost drivers
-
supports operational readiness at an affordable life cycle cost
-
generates availability simulations of product support solutions
If you are a manager, decision-maker, engineer or ILS/IPS team involved in system design, system acquisition, proposal writing, support solution optimisation, in-service support management and through-life support, you need Analyzer for your Life Cycle Cost (LCC) Optimisation, Level of Repair Analysis (LORA), Spares Optimisation, Availability Modelling, and much more!
Analyzer is seamlessly integrated with our LSA (GenS) tool, for the ultimate modelling analysis and LSA functionality.
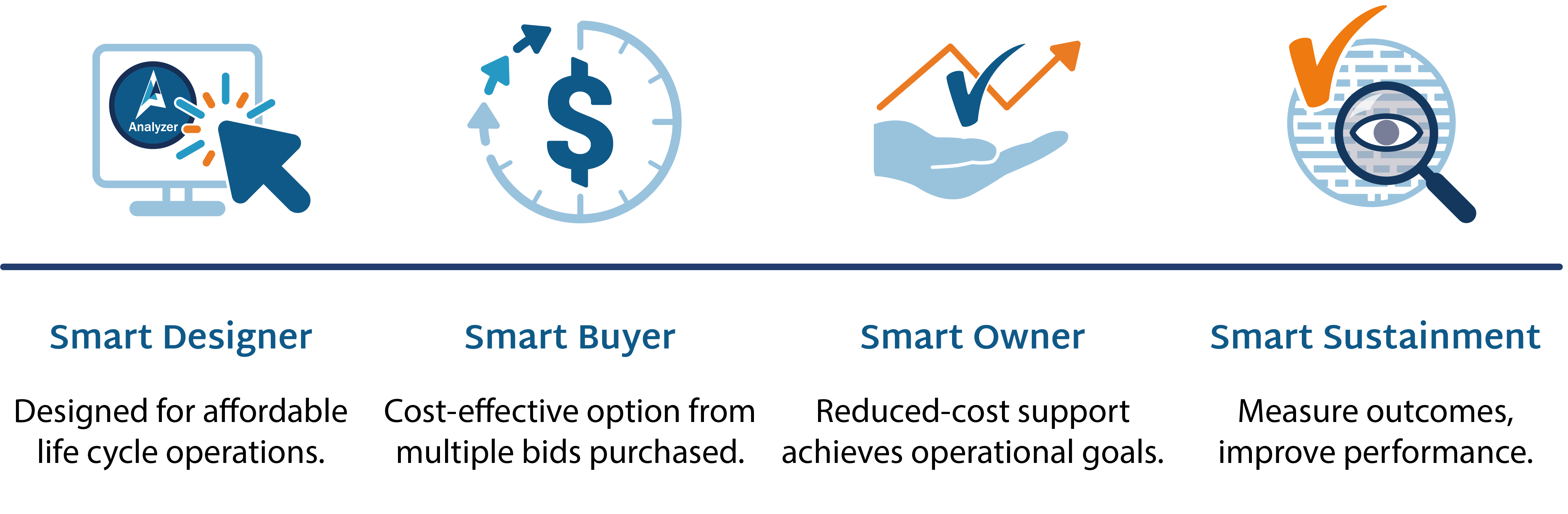
The Analyzer Dashboard
A graphical view of data is very useful when making decisions. Analyzer provides dashboards, including fully user-definable displays, that will present your data in ways that make decision making easier.
Analyzer helps decision makers by presenting the dashboard and reports. The analyst can easily go ’behind’ the dashboard to populate the supportability data sets and provide the alternatives for trade-off and sensitivity analyses. All of the data and refreshing the dashboards is applied through defining operational and support scenarios.

Cost effective product support solutions
With the need to make good decisions when designing and managing a Product Support solution, and a business drive to reduce ownership costs, the challenge of cost-effective equipment support is pushed to the limits.
Analyzer is a software product that provides the power of a modern GUI and the sophistication of the embedded proven algorithms. Analyzer can determine the best repair policy for equipment and reduce the cost of owning spare parts. The cost estimation and prediction support decisions based on Life Cycle Costs (LCC).
Analyzer is either a stand-alone decision modelling tool or integrated with GenS to provide a tool that works with the many international standards of supportability data (eg. MIL-STD-1388-2B, SAE GEIA-STD-0007, DEF-AUST 5692, S3000L) additionally, Analyzer can be aligned with any of your bespoke standards through data exchange.
The LCC model
Determines the Life Cycle Cost (LCC) of an operation and support scenario. The basic cost breakdown structure for R&D, Acquisition, In-Service and Disposal is developed. The cost of allocated spares recommended by the Sparing model is also taken into consideration. The basic model calculations can be extended with user defined cost classes, inflation rates and customised costs. Cost results are analysed by using Sensitivity or Trade-off analyses and by applying cost Risk analysis. The application of project-based cost breakdown structures aligns the LCC results with other project costs.
The sparing model
The Sparing model determines the optimal allocation of the quantity of repairable and consumable spares within a defined logistics support organisation, resulting in, minimum inventory requirements to meet desired availability for least spares cost. It handles replaceable units that will drive the Prime Equipment effectiveness and consumables stocking policies for inventory distribution, reorder points and reorder quantities.
Mission Analysis mode assumes equipment will be sent on a mission for a specified duration and that only on-site maintenance will be possible. This module provides a list of the spares required to maintain the equipment at a specified “Measure of Effectiveness”, such as availability.
The LORA model
The Level of Repair Analysis (LORA) model, determines the most cost-effective maintenance policy for each replaceable unit of a Prime Equipment. LORA examines the operating and support costs for every disassembly and repair option possible within the specified capability of the Maintenance Organisation. After making the initial repair versus discard decision, LORA will select the optimal location for repair of the defective unit.
LORA uses cost estimates based on the LCC model and includes user defined values that are unique to the product analysis undertaken. LORA includes non-economic overrides to drive the repair decision based on operational and support constraints.
Modelling support tasks
Analyzer includes the definition of support tasks to allow for the more detailed modelling of your support solution. Using a Task Library, all parts in the logistical structure can have specific PM and CM tasks assigned. Each task is driven by some trigger (i.e., failure event, scheduled maintenance, inspection) and has task techs and resources assigned.
Using the task-based analysis a more detailed LCC can be estimated, and detailed labour hours determined.
Model based product support
Analyzer is a valuable modelling tool to support your MBPS application. As a through-life modelling capability using the Baseline Comparison System approach to analysis, Analyzer will predict outcomes of alternative solutions during Options Analysis; determine optimal support solution designs during acquisition; and evaluate operational data feedback to assess performance providing improvements during the in service operational life.
Sensitivity analysis
In cases where input data is based on engineering or contractor estimates as opposed to actual data, it is recommended that a study be conducted to determine how sensitive the solution is to variations in some input parameters. Analyzer provides a convenient method of performing sensitivity analysis by providing the user with a wide range of sensitivity factors that are applied at run-time and do not affect the data stored in the databases. Sensitivity analysis can be applied either globally on all values of a parameter or can automatically assess a sequence of changes to a specific value.
Trade-off analysis
Analyzer provides for full trade-off analysis to test the “what if?” scenarios. By comparing the results of a comparative analysis against the baseline, the user can determine the relative merit of different decisions.
Optimise asset maintenance and support solutions by understanding life cycle costs and sustainment resources needed to meet your operational demands.
Want to know more about our products?